BIODIESEL
Biodiesel Plant Design and Production Specifications
The Compro System is designed to produce biodiesel in accordance with ASTM D6751. The capacities vary from 5,000,000 to 30,000,000 gallons per year based on an operation cycle of 24 hours per day for 330 days per year.
Plant Major Asset List
Compro will design and construct the following assets into the plant.
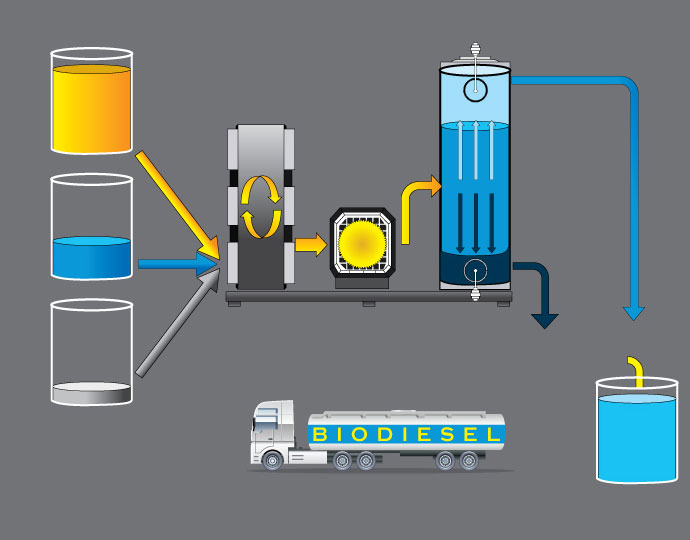
BIODIESEL PRODUCTION
INNOVATION
The ComPro system brings innovation to bio-diesel processing by making much better use of all equipment needed in the process. This results in improved purity of the bio-diesel that will consistently meet all standards, reduce losses and value-added by-products.
Low-value feedstocks have been always been a problem as they typically have high free fatty acids and other catalyst poisons. So using typical cleaning processes proven in the edible oil markets we improve the quality of the base. Then convert the free fatty acids to partial glycerides prior to the reaction to make Bio-Diesel the fatty are recovered and converted to product. Depending on the design of the converter it’s possible that the conversion to methyl esters will be done at high temperatures improving yields and reducing reaction times.
The bio-fuel is distilled so it’s a purer than the solely reacted products and washed products. This solves the cold test problems and improves yields as the bottoms from the distillation process are recycled back to the reaction process.
The glycerin stream is processed to improve the quality and reduce losses. Typically this stream contains high soap as well as waste glycerin. The design converts the soaps back to free fatty acids and recycles this product back to the front of the process. Then the glycerin is distilled in the equipment allowing a waste stream to become a purified value added byproduct.
In reference of swing from one feedstock to the next, our technology does not require any shut down to switch feedstocks because of the short time the feedstock is held at low stripping temperature. This has allowed the development of highly efficient of any continuous distillation processing – An area of excellence for ComPro.
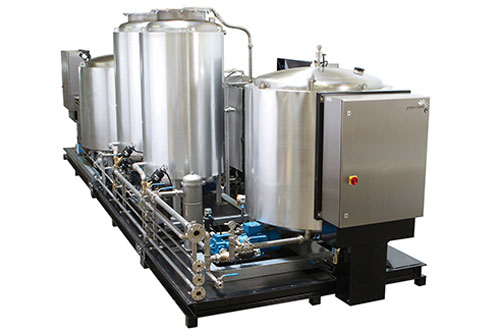
DEGUMMING
This system will dispense both acid solution and soft water into stirred reactor of oil preheated and subsequently held at 180°F. The controls will allow the operation to select the degree of acid treatment based on PPM of acid up to 1500 ppm. Water additions will range from 0-10% of oil volume. The vessel shall be sized to allow 30 minutes of contact time between the water and the acid. The resulting flow will undergo oil/gum separation in a static separator. The resulting gums will be heated and sent to the soap stock Vestment system.
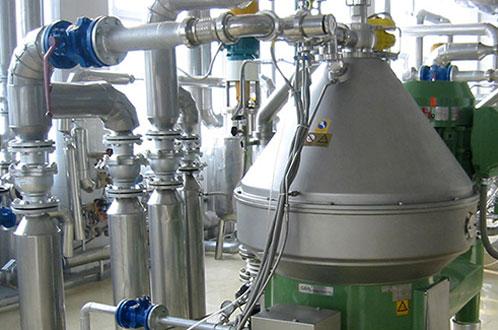
BLEACHING
This system is capable of independently dosing, then mixing, both bleaching clay and filter aid over a range of 0.25%-1.5% proportioned to oil flow. The unit sized to allow 30 minutes of contact time. Each filer system will be sized for 8 hours of operation assuming 1% bleaching clay in the flow. After clay filtration, the oil will go through a sock filter to remove any fugitive clay.
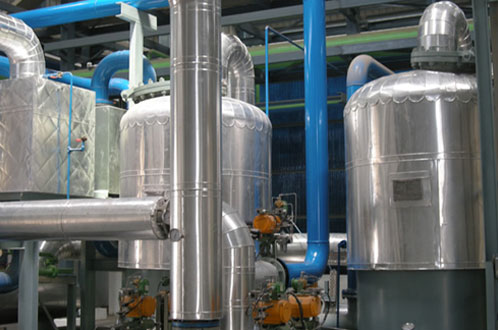
ESTERIFICATION SYSTEM
This is a continuous 3 reactor system with 3 hours of hold time. The system is fed methanol and catalyst under PLC control, and it is capable of reupping the catalyst as the oil leaves the first reactor. This is not a pressurized system running at the boiling point of methanol. The glycerin is decanted off automatically from the bottom of each reactor and off a final static glycerin separator. Methanol is flashed off under vacuum in a controlled loop heating system and recovered in a 15°F recovery condenser (not shown). After distillation the methyl esters are water washed twice using soft water. The wash water is separated using static separating tanks. The water is sent to the soap stock system.
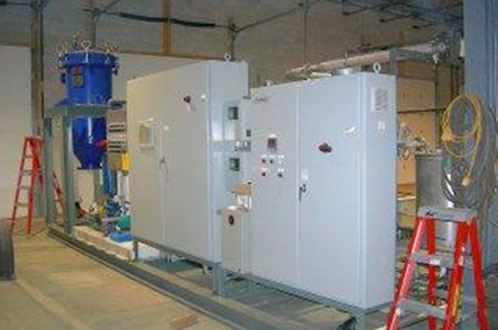
CONTROL SYSTEM
The plant is to be equipped with a PLC control system capable of controlling and monitoring all aspects of the plant necessary for production. This is to include but not limited to recipes, historical data and current plant status. Where necessary the PLC system will have remote operator in put in areas such as dry ingredients loading. In addition to the main operator station the PLC system will have the capability of showing plant status for key operation in 2 areas.
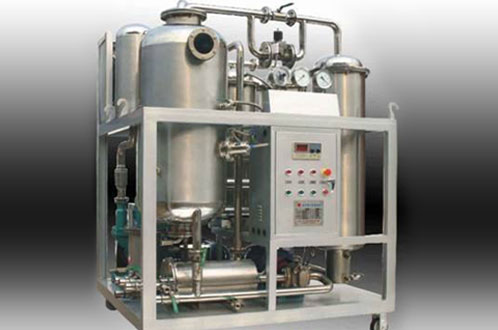
SOAP STOCK TREATMENT
This system is sized to receive and treat all wastewater flows from the other process systems. The system will automatically acidify water, then spilt and return the oils and FFA to the vacuum reactor (Glycerolisis) system. In addition, the system will automatically condition the wastewater stream to
pH 7 for discharge.
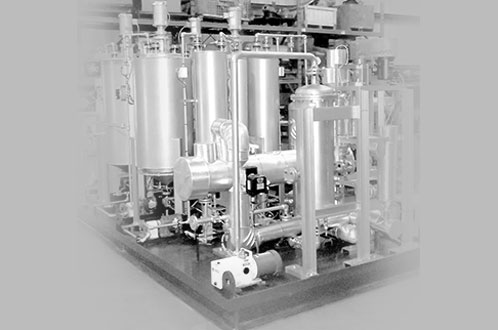
DISTILLATION SYSTEM
This covers both the flash removal and steam removal of the methyl esters. This system will flash off 50% of the methyl esters and steam strip the balance in the Compro distiller. The flash tanks and the distiller are sized to allow 50% return and still meet the total plant output. The system will have controls to manage input flows, recirculation flows, vacuum and heat for both the flash tank and deodorizing system.
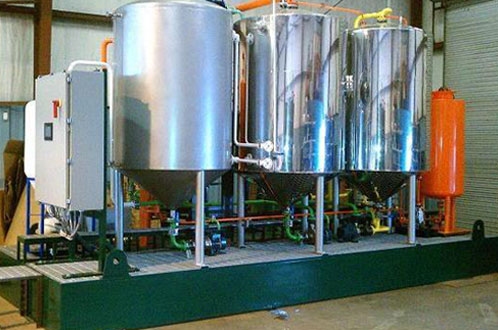
GLYCERIN REFINING SYSTEM
This system removes the methanol from the glycerin, and then flash distills the glycerin itself. After distillation the glycerin is mixed with bleaching agents and finally filtered. The distillation and flash tank are sized at to work in lockstep with the esterification system. The bleaching system has 3x that hold capacity and is only run once a day. The condensate from the vacuum system will be sent to the soap stock system.
This system has its own vacuum system and scrubber to prevent cross contamination. The product of this system is USP grade glycerin.
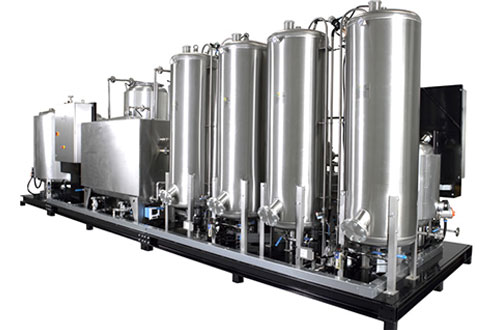
METHANOL VAPOUR SYSTEM
This will be two cold traps running at 15°F, using direct evaporation Freon. Methanol vapor will be captured in the first trap and sent to the methanol day tank. All other plant vapors are directed to the second trap for capture. The system is driven by a liquid ring vacuum pump using a closed loop of methanol as the liquid ring.